Success Stories
Reduced product loss and avoidance of safety problem
Problem : Lighter Hydrocarbon product loss in Distillation column bottom stream was remaining higher side (above 3 % by wt. to against 1.5 % by weight causing safety risk of bottom stream storage tank pressurization.
Suggested change in Control philosophy based on Aspen simulation model.
Revised philosophy implemented resulted in maintaining losses less than 1 % by weight.
Resolved safety issue and Monetary benefit Rs. 1.2 Crore per annum
Increased Production by 45 %
Problem : Production capacity to be increased over 45 % having five product column purification plant. Consultant suggested to put additional column with condenser and reboiler to meet product quality at higher capacity.
Process Flowsheet developed in Aspen for Purification plant. Based on sensitivity study, all column parameters are optimized to meet same product quality at higher production (45%) capacity.
Avoided 4 Crore investment as well as supervision requirement by Panel engineer for new set up.
Improved product quality to avoid revenue loss
Problem : Process plant was designed for 98.4 % product purity. Customer demanded for product purity higher than 99 % or discount due to availability in market due to globalization.
Initial study by consultant envisaged investment of Rs 5 Crore for additional column facility as well as supervision requirement by Panel engineer for new set up.
Suggested change in Control philosophy based on Aspen simulation model.
Revised philosophy implemented resulted in higher purity product (99%) in same column without any additional investment and avoided revenue loss.
Batch process to continuous process
Problem : Process plant was designed to have product purity of 99.7 % by wt. from two alternative feedstock having 26 % by weight and 95 % by weight product content. Hence, depending upon feedstock availability changeover philosophy of batch mode operation was being practiced.
Based on total plant simulation model, proposed to process feed having 95 % by weight product content at appropriate location to have continuous processing of both feedstock.
This has helped in reduction of energy/hydrocarbon loss occurring during changeover process and avoided human intervention of changeover process.
Power and Steam Network Optimisation
Problem : Identification of energy conservation schemes for Power and steam generation plant.
Aspen models developed for Power and Steam network including Gas turbine, steam turbine, boiler and HRSG.
Optimized boiler parameter for existing operation to generate additional 260 kw power generation. (Saving Rs. 2 to 2.5 crore per year without any investment)
Based on Power and steam network analysis, microturbine for power recovery of 146 kw installed. Further additional 150 kw power generated with same turbine with change in operating parameter. (Total saving is Rs. 2.5 to 3.0 crore per year)
Dynamic Simulation Model for Column Stabilised Operation
Problem : Unstable column operation due to feed quality and throughput variation resulting variation in product quality.
Dynamic simulation model developed in Aspen HYSYS. Various control philosophy tested for various disturbance and robust control philosophy implemented. This ensured consistent bottom stream composition and no human intervention for column performance.
Batch Process modelling for environmental concern
Problem : In a batch process of solvent recovery having azeotrope with water, hydrocarbon loss in water was resulting in environment concern.
Batch processing model developed in Aspen plus. Batch cycle time minimized with batch-cum-continuous operation. Reduction in cycle time used to process collected waste water at end of the different batches to recover solvent and minimized hydrocarbon content within environmental norms.
Rs. 12 lacs saving per month in addition to resolution of environmental concern.
Utility optimization for increased production capacity
Problem : In one of the plant the process equipments are adequate for increased capacity of the plant. Since different refrigeration systems were limiting, it was necessary to have additional capacity which require large investment.
Detail study of refrigeration systems alongwith cooling water system done to improve the utility performance. Based on study only one cooling tower cell added and one condenser installed in one of the refrigeration system.
This has helped to increase production by 12.5 %.
Since the contribution is very high further 5 % production to be increased without major investment for process equipment and utility system upgradation.
Heat recovery beyond Pinch Technology
Problem : It was necessary to reduce specific energy consumption for one old vintage plant to make it competitive.
Detail Pinch study was carried out to identify heat recovery schemes. Accordingly various schemes were implemented. In recovery section, one heat recovery exchanger installed in upstream of first column feed preheater to minimize the steam consumption of existing feed preheater. The hot stream utilised in new exchanger is second column overhead vapor. The scheme has reduced the heat load by 12.25 % of total heat load of recovery section.
However, based on recovery section modelling, it was found that further 35 % heat recovery is possible with new installed exchanger by revised separation philosophy. The benefit of the scheme is Rs. 3 crore per year to Rs 4 crore per year depending on energy cost.
Use of surplus steam
Problem : Due to envisaged heat recovery, higher steam (low level steam, 6 to 7 MT/hr) generation was expected. But as per complex steam requirement, it was becoming surplus and need to be vented.
Detail study of complex steam network done to find out various alternatives like change use of steam(low level) instead of low medium level in reboilers (not feasible based on adequacy check) , Installation of Thermocopressor (high payback due to higher Investment) and use in direct process heating (minimum investment).
The scheme of use of surplus steam in direct process heating implemented which reduced low medium level steam which was generated though PRDS from High pressure steam. This has reduced steam generation requirement at Boiler. Saving is Rs. 7 crore per year.
Use of redundant column for new product
Problem : A plant revamp was done to increase capacity as well as one more product as a bottom stream of the column along with main product as a top stream. The new product purity and production could not be achieved due to wrong assumption of separation efficiency consideration at design stage.
The simulation study using ASPEN carried out to explore use of one redundant column. Different option of series or parallel, sequence change, feed preheating/subcooling etc. have been evaluated for feasible solution. Special tray arrangement designed for redundant column to make it adequate for required vapor/liquid loading. The major challenge was new product should have less than 20 ppm of main product as impurities.
After installproduction of both products achieved as per desired purity and capacity.
Office
B-11, Chankyapuri, Sama,Vadodara, Gujarat, India. PO: 390008
Contacts
process-energy@kkparmar.in
+91 9998217287
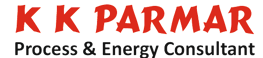
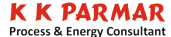
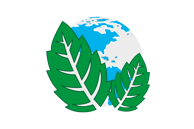
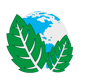